|
 |
|
 |
 |
 |
The Care and Use of Synthetic Waterstones |
posted on 6:04pm by David |
|
A guide to tool sharpening and stone preparation and maintenance.
Introduction
A number of Japanese firms manufacture synthetic water stones. After many years of experience, we have discovered those brands which offer the most consistency in quality, cutting effect, and value to the user. Generally speaking, synthetic water stones can be classified into three groups: Very coarse stones for the maximum removal of metal, medium coarse stones for refining the edge and establishing the "burr", and finish stones for final honing and polishing of the edge. Very coarse stones are available in #80 to #400 grits. Medium coarse stones are available in #700, #800, #1000, #1200, #1500 and #2000 grits. Finish stones are available in #3000, #4000, #5000, #6000 grits. Polish stones are available in #7000, #8000 and 12000 grits. And Shapton makes a #30000 grit super polishing stone.
In addition to different grit sizes, we offer stones in a variety of abrasive materials and manufacturing methods. Generally speaking, the more expensive the stone, the faster it will cut per grit size and the longer it will last. The abrasive types are aluminum oxide, silicon carbide and chromium oxide. All of the stones, except for the Debado series are heated at high temperature to fuse together the abrasive particles in a porous matrix. The Debado Stones are chemically cured in a precisely temperature controlled humid environment.
A typical sharpening sequence is to first establish a flat bevel and remove any nicks with one of the very coarse or medium coarse stones. The choice of grit depends basically upon how much material needs to be removed from the bevel in order to leave a clean, true edge. If there are no nicks or other defects, the #1200 or perhaps #2000 grit stone is the best choice. However, if more metal needs to be removed the #700, #800 or #1000 grit stones cut faster. This of course means less effort will be required.
The #80 through #400 grit stones are the best choice when a considerable amount of metal must be removed. Keep in mind though; these stones will leave scratches which must be removed with a medium coarse stone prior to final polishing.
After the medium coarse sharpening is completed and a "burr" is obtained, the tool is transferred to a finish stone and alternately honed on back and bevel sides until the "burr" is totally removed. Finishing or polishing can be accomplished in one step, with any stone from #3000 grit to #8000 grit. However, in general, a better edge will be obtained if the tool is first honed on a #3000 or #4000 grit stone prior to final polishing on #6000, #7000 or #8000, 12000 grit stone.
Debado Stones
As noted above, the Debado Stones are manufactured by a different process and do not require soaking in water prior to use. You need only apply a handful of water to the stone surface to begin sharpening. Please be aware that these stones will deteriorate if left in water. As with natural stones, the Debado Stone may occasionally develop small fissures. These fissures are normal and do not affect the sharpening qualities or cause any deterioration of the stone.
Shapton
Shapton Water Stones are color coated to enable the user to avoid mixing up grit sizes and do not need to be soaked prior to use. Simply splash a handful of water on the stone's surface and start sharpening. Shapton stones should be stored dry. If left in water they will begin to deteriorate over time. Otherwise use as described below.
Preparing Stones for Use
Except for the Debado Stones, all of our synthetic water-stones must be soaked in water for several minutes prior to use.
You will see the bubbles rise to the surface as the stones absorb water. The very coarse and medium coarse stones, except for the Debado Stones can be left permanently in water without damage to the stones. However it is always best practice to remove finish stones from the water after use. Under no circumstances should any oil based lubricant be used, as this will ruin the stone. A few drops of Charlie's Soap added to the water will help improve the cutting effect of the stone.
It is very important when sharpening chisels and plane irons that your stones be flat. Checking for flatness is particularly important, since any irregularity in the surface of the stone will be transferred to the tool's edge. After a bit of experience, you will be able to tell by visual inspection whether or not the stones are flat, or you may use a straightedge for this purpose.
How to Flatten Your Stones
The easiest method to flatten a coarse stone is to rub it across wet/dry sandpaper placed on a flat surface. If your stone is fairly flat, #220 grit paper is sufficient. However, if a greater amount of material needs to be removed, then a coarser paper such as #120 grit is appropriate. The finish stones are easily flattened by rubbing them together with a previously flattened coarse stone. At this time, it is a good idea to sand a 45° bevel on the 4 top edges of the stone. This prevents "pressure flaking" of chips from the sides of the stones.
How to Sharpen
Now that your stones are saturated with water and flat, you are ready to begin sharpening. Place a coarse stone on a flat, secure surface so that it will not shift during use. Begin rubbing the tool back and forth on the stone. Allow the "mud" to build up and remain on the surface. This will give a better sharpening effect and ultimately, a keener edge. Should the stone's surface begin to dry out during sharpening, add a finger-tip or two of water to the surface. As soon as a wire edge or "burr" is obtained, transfer to a finish stone and complete honing of bevel and back side of the blade. Proceed on the finish stone as already described for the coarse stone.
If the tool requires a considerable amount of sharpening, periodically check to ensure that the stone's surface is flat. If not, flatten as previously described.
Blue Stones (Ao Toishi)
For the finest edge, it is suggested a Blue Stone "Ao Toishi" be used between the coarse stone and the finish stone. There are now two types of Ao Toishi: the original "mountain blue" natural stone and the new "Nonpareil" synthetic stone. Blue Stones are used to remove the scratches left by the coarse stones. This improves the polishing action of the finish stone, giving a sharper, longer lasting edge. In addition, Blue Stones can be used to touch up an already keen edge (by Western standards) before re-polishing on the finish stone.
Nagura Stones
The incredible polishing action of a finish stones results from the 'mud" which builds up on the surface of the stone during honing. Nagura Stones create this mud before honing begins, thus speeding up the polishing process. In addition, the Nagura Stone makes the stone surface slipper, keeping the tool from sticking. Nagura Stones are small pieces of very fine natural stone, specially mined for this purpose. Now a day, manufactured Nagura stones are available.
A Nagura Stone is easy to use. Simply rub it in a circular motion on the full surface of a finish stone until a paste develops. If the stone surface is too dry the Nagura Stone will stick. To alleviate this problem, add a few drops of water. Generally speaking, the more paste, the better the honing action.
Water Stone Base
Below is a drawing of a Japanese style base which is used to hold water stones steady during sharpening. The base is easy to make, and the user can vary the design to suit his taste. Redwood or cedar is typically used. However, any water and warp resistant woods are suitable material.
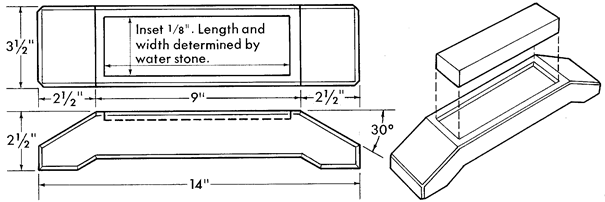
Comments (0)
|
|
|
 |
|
 |
|
|